Cement facilities must be decarbonized if we are to achieve our climate targets. It is an essential component of concrete, the world's most frequently used artificial substance with few, if any, viable alternatives.
But there's a catch, it is highly polluting to produce: while it only accounts for 10-15% of the mass of concrete in a typical mix, it contributes up to 90% of the greenhouse gas emissions.
Pollution from the Cement Industry
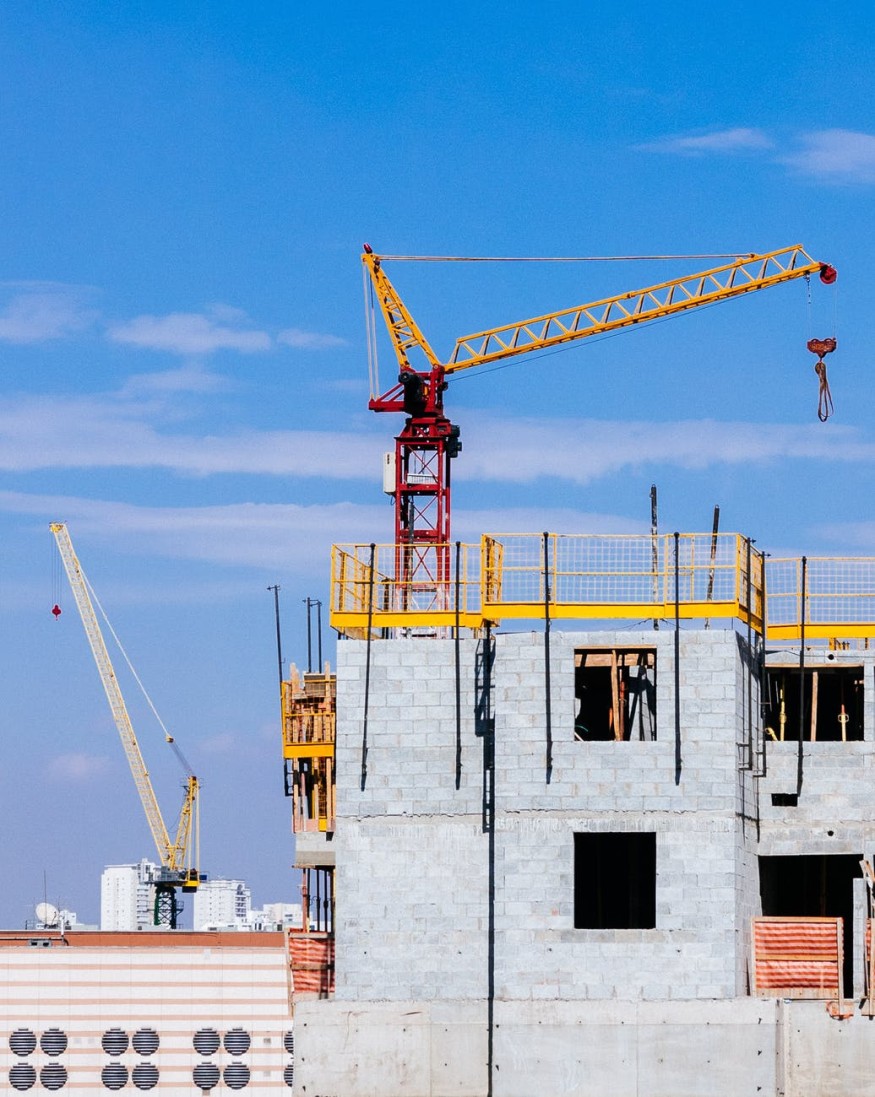
If the cement industry were a country, it would be the fourth greatest emitter of greenhouse gases globally, trailing only China, the United States, and India and responsible for around 7-8 percent of worldwide CO2 emissions. As the demand for concrete continues to grow, this amount is expected to rise unless we decarbonize cement.
The cement industry is the third greatest producer of industrial air pollution, including sulfur dioxide, nitrogen oxides (NOx), and carbon monoxide, and is associated with a wide range of health problems.
If we want to achieve our climate and health goals, we need to clean up the cement sector. However, unlike the internal combustion engine, cement has no readily available substitute that can scale up rapidly enough to satisfy the climate crisis's demands.
As a result, while reducing and substituting Portland cement with existing and emerging alternatives can and should be a priority, as urbanization and infrastructure renewal accelerate, our reliance on the material will not only continue but likely increase in the coming decades - the most critical timeframe for climate action - as our reliance on the material increases.
The need for us to promote cement manufacturers' adaptation to a cleaner future arises due to this.
Related Article : How Bamboos Can Help Make Modern Construction More Sustainable
Taking Actions
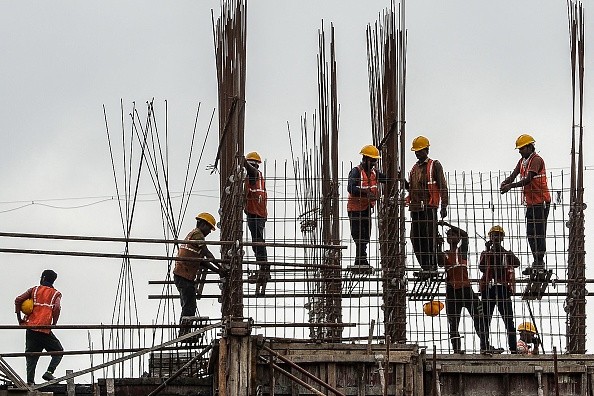
The good news is that momentum is rising in states and federally, as politicians explore creative ways to reduce cement production's emissions and use the government's purchasing power to expand markets for cleaner alternatives, as well as leveraging the government's purchasing power.
Commitments and roadmaps for achieving carbon neutrality in the industry are also rising. While some of the decarbonization solutions used by some cement makers are highly harmful to the environment and/or public health, it shows that the industry recognizes the need to have a strategy to reduce emissions.
As these initiatives progress, one of the essential principles that NRDC advocates for are that lowering cement-related carbon pollution should not come at the price of local pollution.
Carbon Footprint
The great majority of the carbon footprint of Portland cement is due to two parts of the production process. Cement is created mainly by heating limestone (raw material) to extremely high temperatures (2,640°F/1,500°C) in cement kilns, similar to enormous furnaces.
The heat causes a chemical reaction in the limestone, which turns it into a clinker, which is subsequently mixed with gypsum to make cement. 40% of the total CO2 emissions in cement (commonly referred to as embedded emissions) come from the combustion of fossil fuels calcination) happens when the limestone is heated, releasing CO2 from the calcium carbonate in the limestone (calcination) is an inevitable chemical reaction (calcination).
Hazardous chemicals such as mercury and criterion air pollutants are emitted in fuel- and process-related emissions.
Premature mortality, neurological difficulties, asthma, and other respiratory disorders have all been related to these contaminants. The cost of certain alternative fuels pushed by industry is excessively high for communities.
Shifting
Switching to solid waste fuels to replace fossil fuels in cement kilns is one of the most commonly stated levers for decarbonizing the cement sector.
Plastic and solid waste, such as tires (also referred to as "tire-derived fuel"), which produce very harmful, poisonous emissions, are included in these alternatives, which are typically labeled as "low carbon" by the cement industry.
One of the most frequently mentioned levers for decarbonizing the cement industry is switching to solid waste fuels to replace fossil fuels in cement kilns. These alternatives, which are often marketed as "low carbon" by the cement industry, include plastic and solid waste, such as tires (sometimes referred to as "tire-derived fuel"), which emit highly hazardous, deadly pollutants.
For decades, communities have fought toxic pollution from cement factories. The Natural Resources Defense Council (NRDC) has argued that reducing carbon emissions without increasing hazardous pollution is possible and necessary. As a result, as a decarbonization strategy, NRDC opposes using fuels that emit harmful emissions, such as plastics and other wastes, to power cement kilns.
Also Read : Advancing Transition to Renewable Energy Should Include Honest Discussion of Costs, Supply, and More
For more news about making the environment sustainable, don't forget to follow Nature World News!
© 2025 NatureWorldNews.com All rights reserved. Do not reproduce without permission.